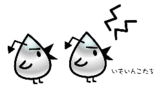
こんにちは、はんだ付け職人です。
今週も引き続き、
はんだ付けを工程審査、工場監査の面から
考える・・の第12回目です。
今日は、「10:クレーム管理」の続きです。
10:クレーム管理
10―2:クレームの対策内容は、真の原因を追究し、
対策を実施しているか?
ここは、発生原因に対する技術的な対策と、
流出原因に対する管理的な対策が実施されているか?
がポイントになります。
作業標準類への反映なども
重要なポイントです。
再発があった場合は、
真の原因をつかみきれていないことになりますね。
先週紹介させていただいた
「クレーム処理票」のサンプルには
「なぜ?なぜ?なぜ?」と原因を
深堀りして考えるフォーマットになっていましたが
不具合発生に至った、真の原因を突き止めて
対策を打てたかどうかを問われます。
実際の監査では、保管された「クレーム処理票」の内容と、
現場での対策の実施状況を比較されることになります。
よくあるのは、新の原因を掴みきれておらず
机上の空論で対策を打ったものの
現場では、「なんの対策にもなっていない!」
として対策が無視されることです。
対策後のフォローを怠ると、いざ監査の時に
「えっ!やってないの?」
と冷や汗をかくことになりますのでご注意です。
10―3:クレームの発生内容、回答の内容について
品質管理責任者が確認し、
必要な指示をおこなっているか?
クレームが発生したこと、
クレームの内容について、
品質管理責任者が知らないようでは困ります。
製造部門に任せっぱなしではいけません。
「クレーム処理票」の処理ルートには
必ず品質管理部門を加え、
品質管理部門で原因・対策の確認を行います。
また、必要ならばライン停止などの
指示を出します。
10―4:品質管理責任者が
クレームの対策結果を確認しているか?
報告を受けて指示を出したまま
放ったらかしになっていないでしょうか?
その後の、フォローができているかを
問われています。
対策品の第一ロット製造時、
または、定期的製造部門パトロールで
立会いにより品質確認を行い、その記録を残しておきます。
「クレーム処理票」の処理ルートに
現場確認の項目を加えておくのも良い方法です。
(サンプルのクレーム処理票には加えておきました)
続きは、また来週。
来週は経歴管理です。
では、明るいハンダ付けを!